Production
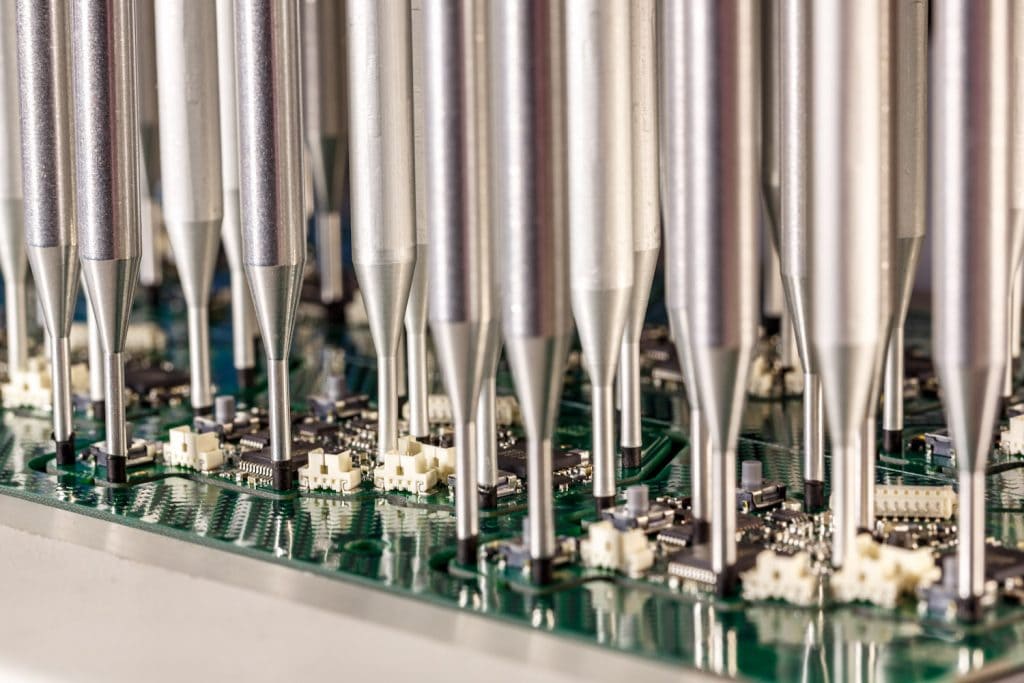
Production Test System
Incorporating a test system into the production process is essential for identifying defects early, delivering high-quality products to customers, and safeguarding the company’s reputation.
Provide Your Information
Enhancing Quality and Efficiency in Manufacturing
A production test system is essential for hardware testing, comprising measurement instruments, fixtures, test software, programming tools for loading software onto products, documentation, maintenance plans, support, and more. Its primary goal is to detect errors during manufacturing, as addressing defects early significantly reduces costs. Allowing faulty products to reach the end customer can be expensive and damaging to both finances and reputation.
The ideal solution for your production test system depends on your production volume and product complexity. With extensive experience, a wide range of tools, and numerous developed test solutions, we can quickly identify and deliver the right system for your needs. Our expertise covers test systems for all types of products.
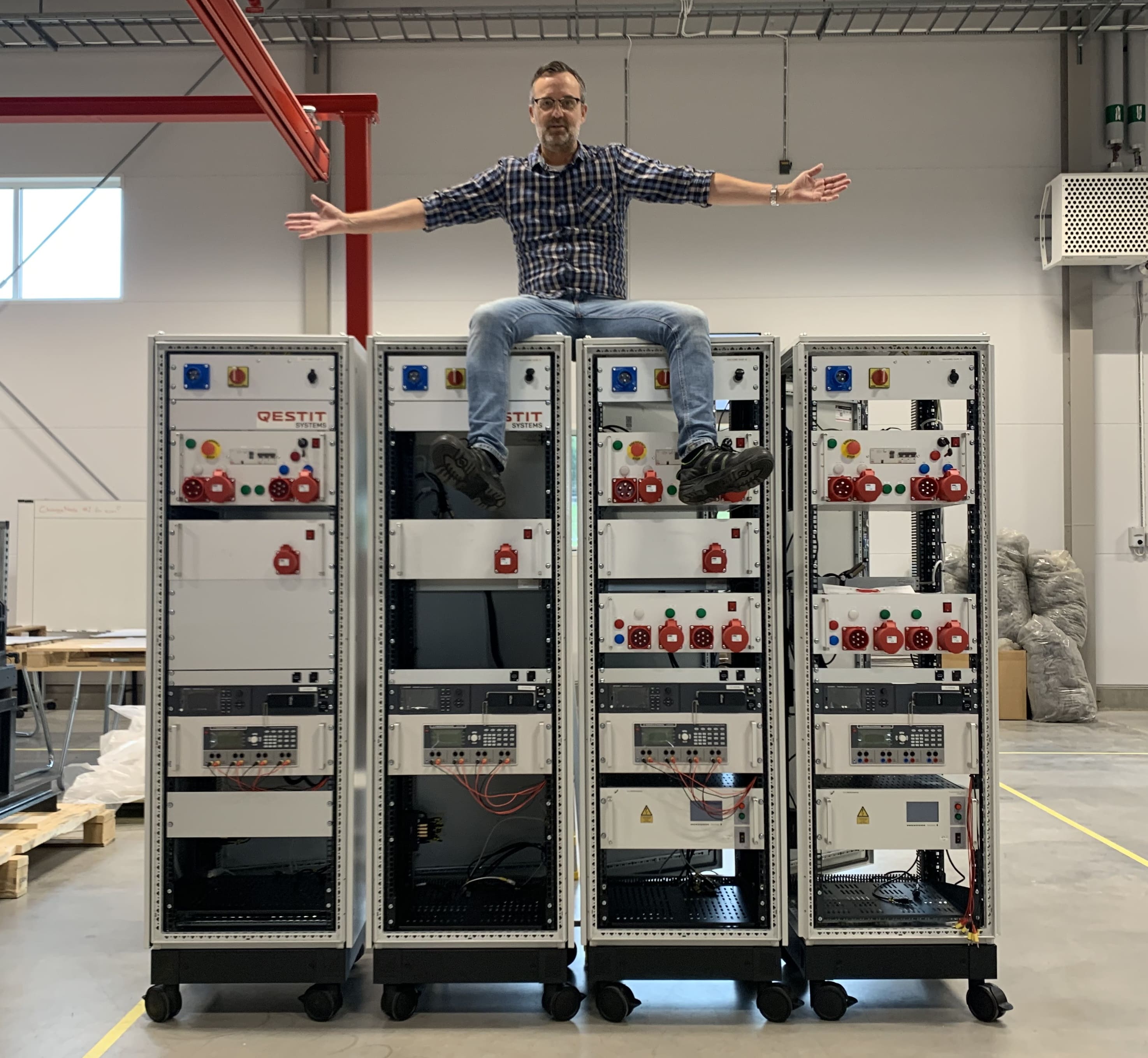
A dependable test system ensures consistent quality, reduces overall product and maintenance costs, and enhances customer satisfaction. We partner with you to design, develop, install, and maintain a comprehensive test system tailored to your production needs, from initial concept to results management.
Whenever possible, we leverage solutions proven successful in previous projects. Reusing software, test procedures, and measurement methods we’ve developed allows us to focus on the unique customer- and product-specific requirements of your test systems. For hardware, we source cabinets, fixtures, and instruments from trusted suppliers like Columbia Elektronik, Elpro, and National Instruments.
Our test systems are built using QATS (Quality Automated Test System), our robust software platform refined over a decade with valuable customer feedback. QATS is a flexible and powerful solution, capable of both sequential and parallel testing, and is adaptable to a wide range of industries. Discover more about QATS here.
Prevent defects further down the line
The process from requirements to delivery
Specification of Requirements
In this phase, we define detailed requirements for the test system to ensure your products meet the highest quality and performance standards. Metrics like durability, electrical properties, and functionality under load are specified, while ensuring the system handles high production volumes with consistency, reliability, and efficiency. Our goal is to deliver a solution tailored to your current and future needs.
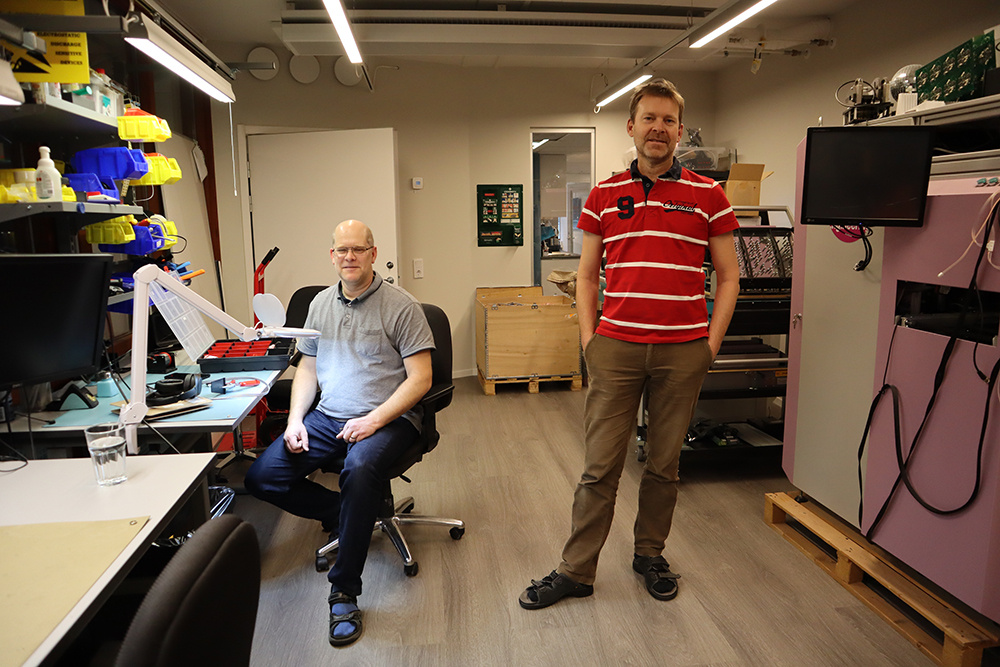
Quotation
We prepare a customized quotation based on your specific requirements, including a detailed cost breakdown for hardware, software, and integration. The quotation identifies suitable suppliers and technical solutions while evaluating their ability to meet current production needs and adapt to future product developments.
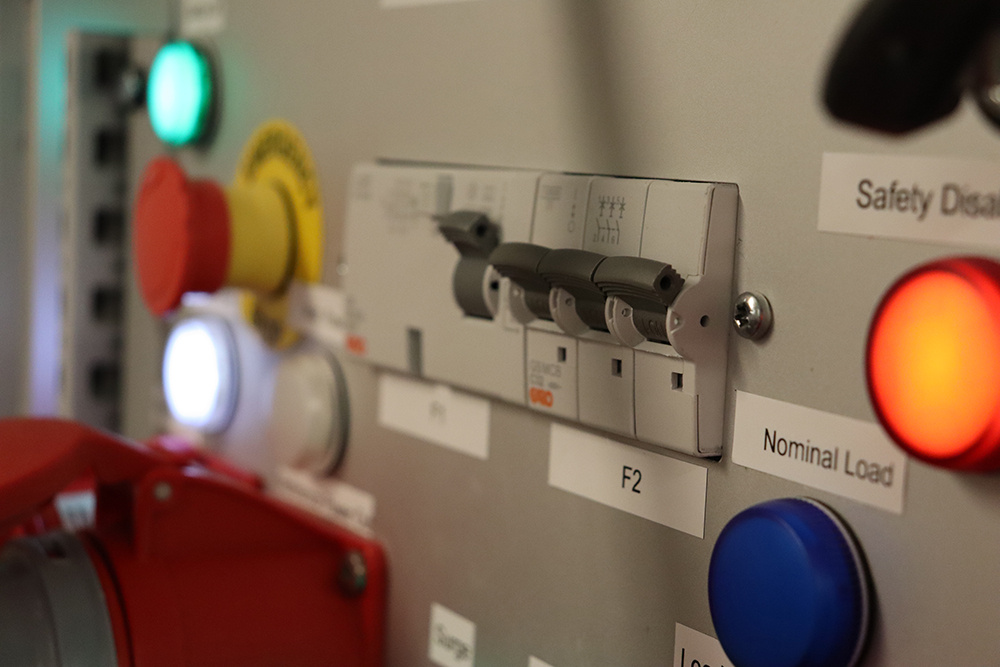
Order
Once the requirements specification and quotation meet your approval, we move forward with the order. At this stage, we finalize all details, including delivery schedules, technical specifications, and quality standards. The contract may also outline milestones for partial deliveries and payment terms tied to specific project phases.
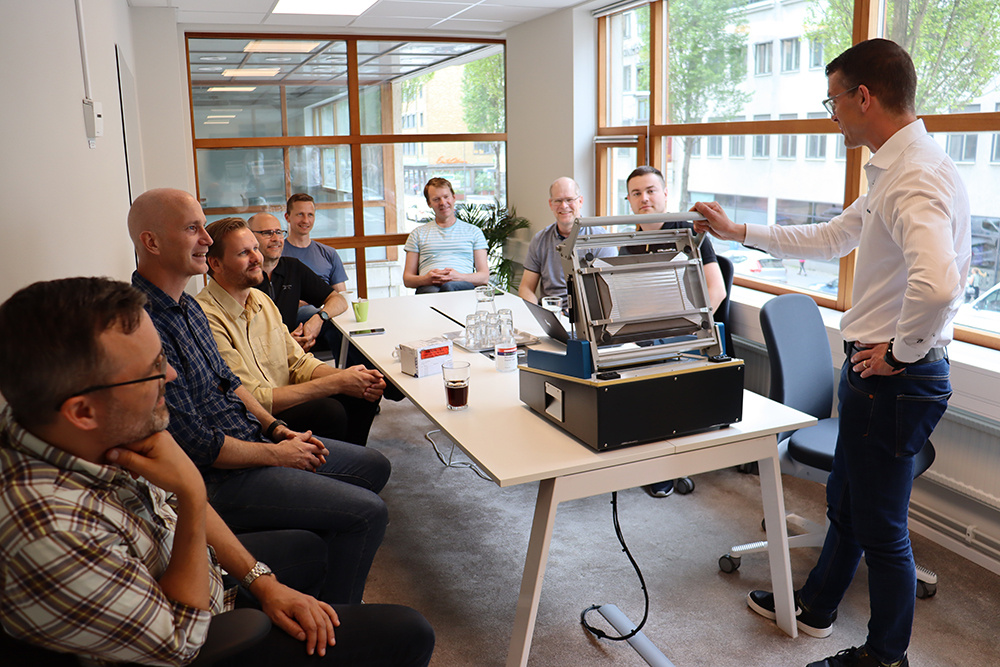
Procurement
In the procurement phase, we acquire all components and resources needed to build and configure the test system. This may include specialized test equipment, custom jigs, and high-quality sensors tailored to production requirements. We ensure all materials meet industry certifications and are delivered on time to prevent delays in the build phase.
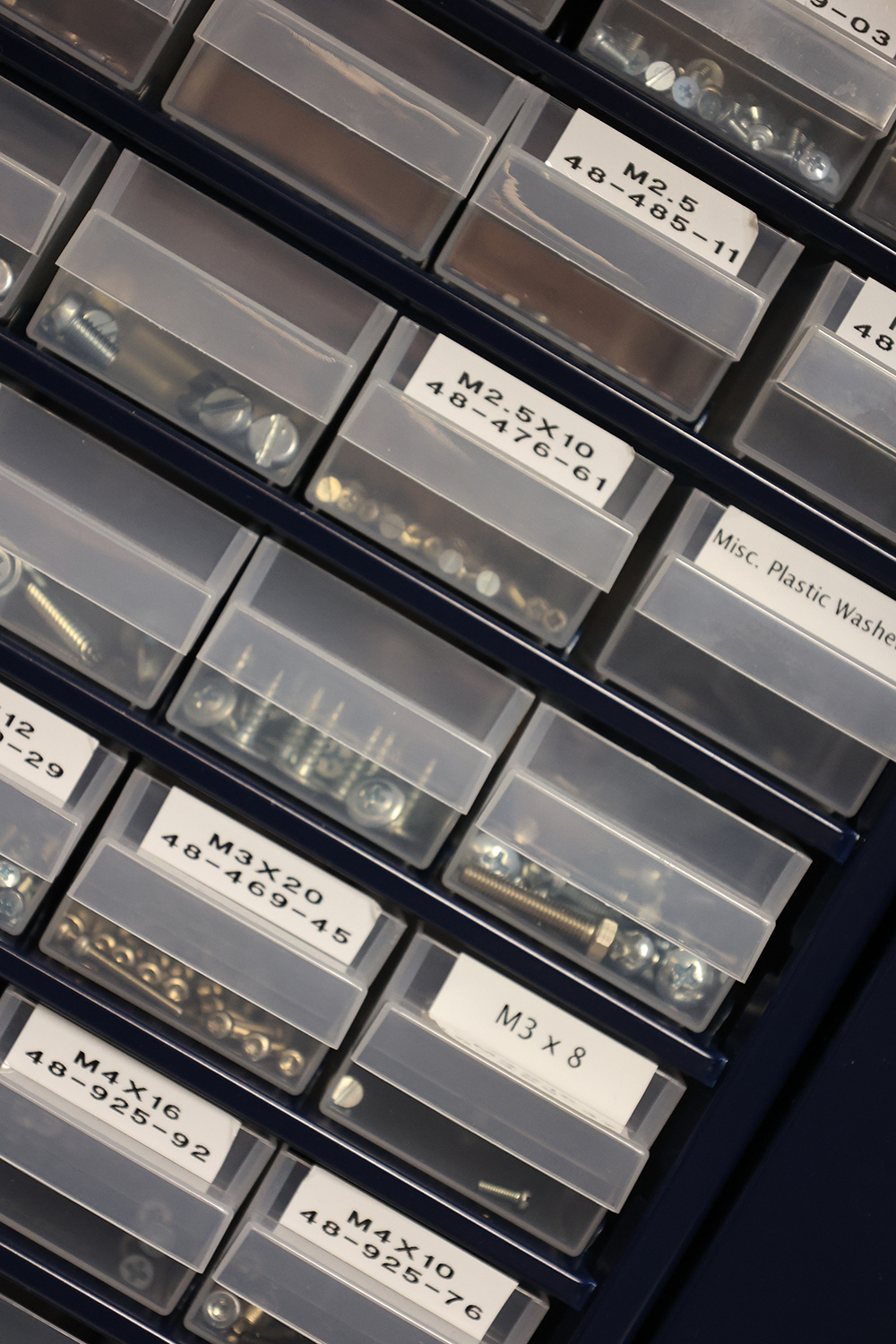
Construction
At this stage, your test system takes shape as mechanical, electrical, and electronic components are assembled and integrated according to the design. Ongoing checks ensure the system meets all specified requirements and functions as intended. Any issues or deviations are promptly resolved to guarantee a smooth transition to the production phase.
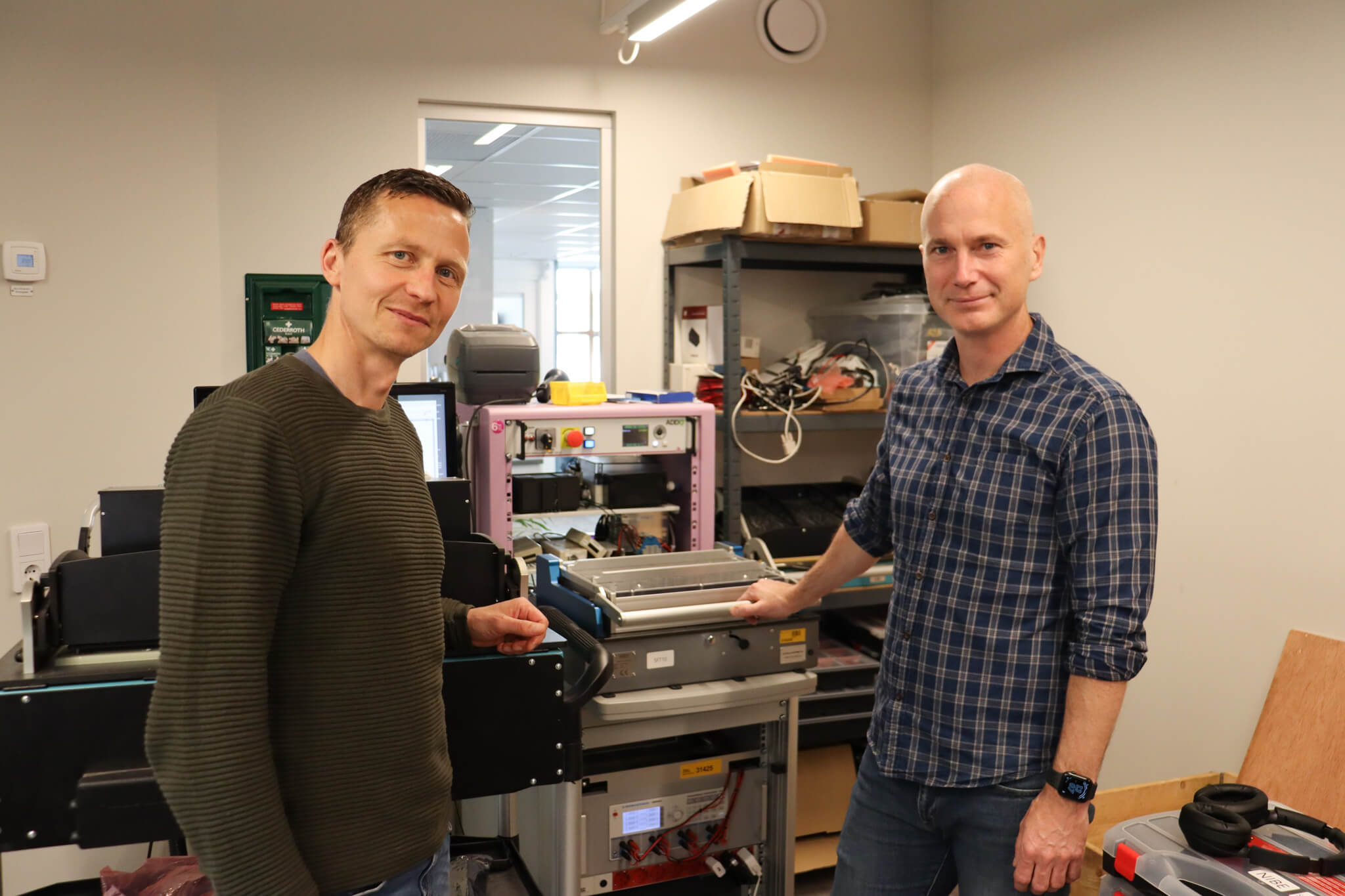
Software Development
While the hardware is being assembled, we develop the software that drives the test system. This software is customized to automate testing, perform real-time data analysis, and deliver clear, rapid feedback to operators. Additionally, we incorporate features for fault reporting and monitoring to ensure optimal product quality and seamless operation.
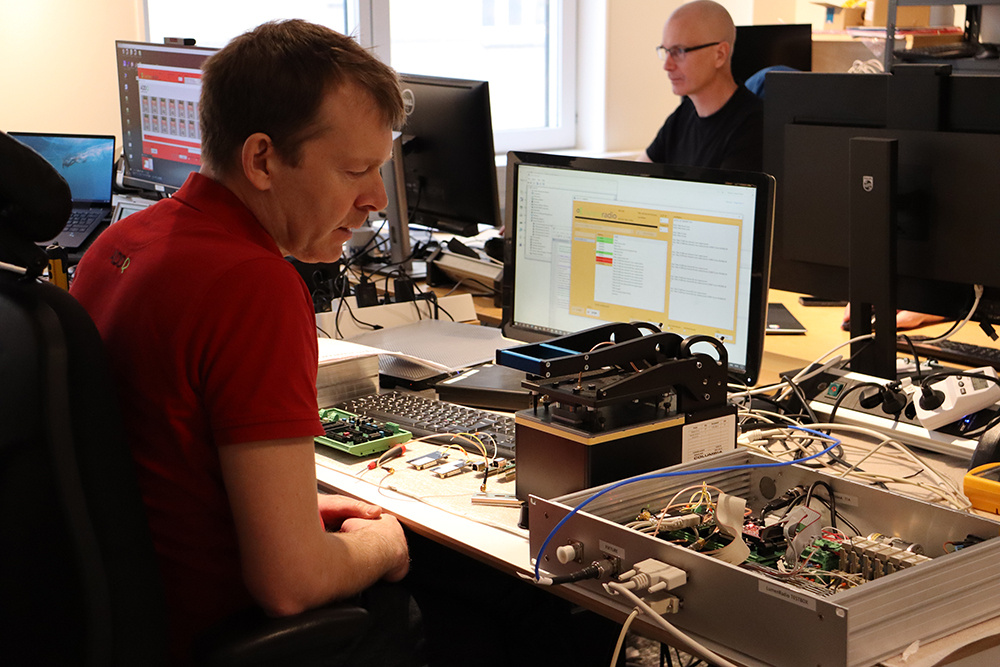
Verification
In the verification phase, the test system is rigorously tested to confirm its performance under real production conditions. Simulated production cycles and stress tests are conducted to identify potential weaknesses. The system’s performance is evaluated against the original requirements, with adjustments made as needed to optimize accuracy, speed, and reliability.
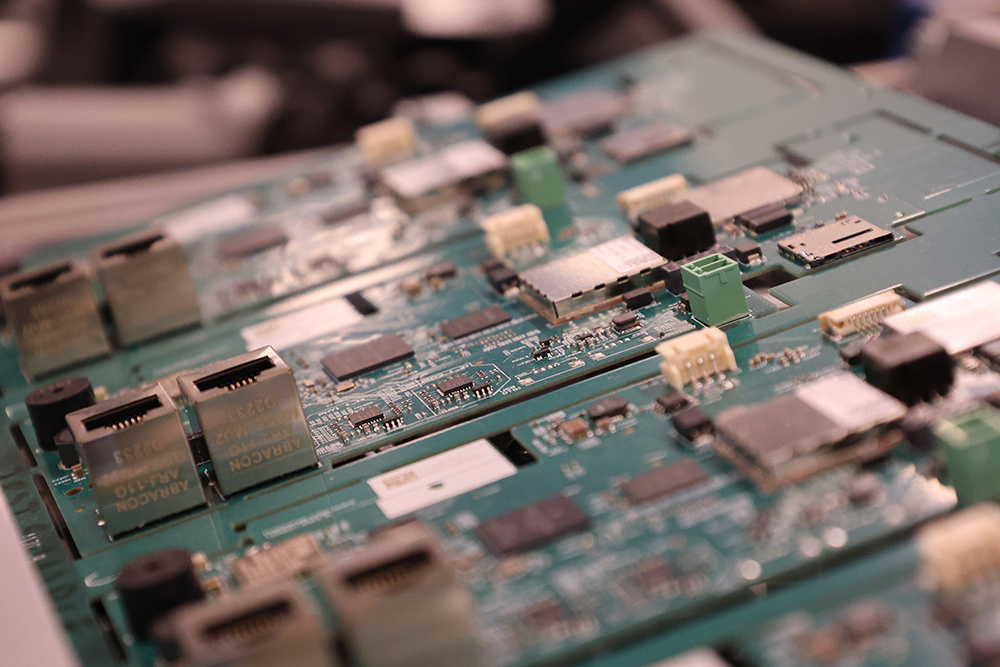
Delivery
Once verification is complete, the test system is delivered and installed in your production environment. This includes both physical setup and integration with existing production lines. Final on-site testing ensures seamless operation in the real-world setting. We also train your production staff to use the system efficiently and provide guidance on routine maintenance and troubleshooting.
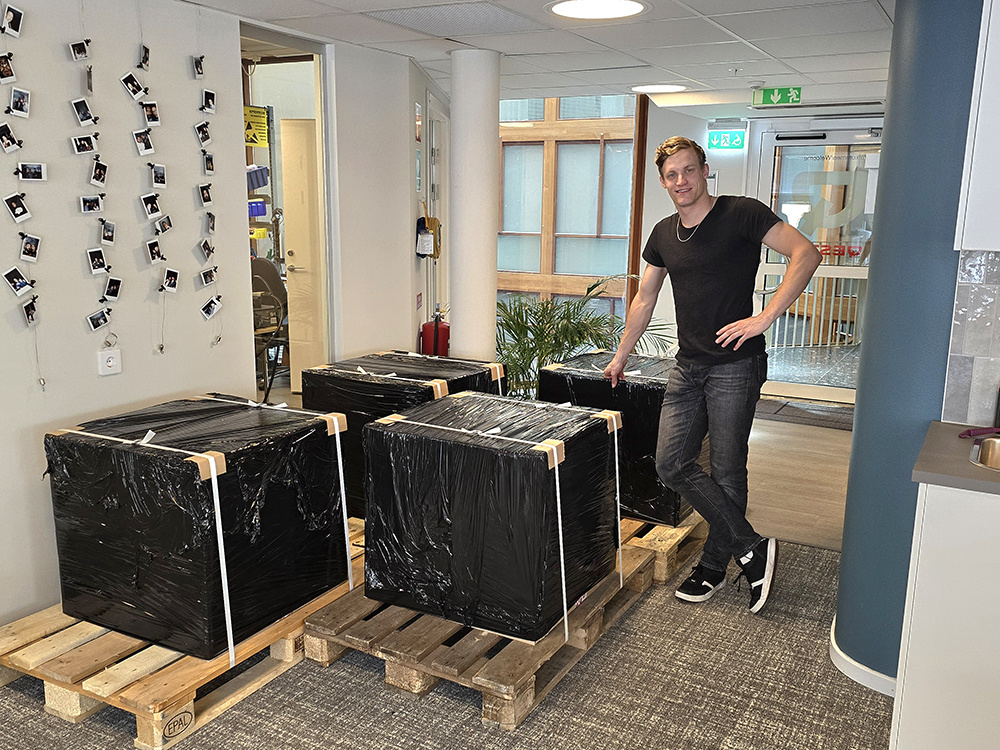